Robotics in the Construction Industry: New Developments & What to Expect in the Near Future
The construction industry is experiencing a technological revolution, and robotics is at the forefront of this transformation. From automated bricklaying to robotic arms assembling prefabricated structures, innovative machines are improving efficiency, reducing labor shortages, and enhancing safety on job sites. In this article, we explore how robotics is already shaping construction and what advancements we can expect in the near future.
Robotics in Prefabricated Construction
Prefabrication is one of the areas where robotics has made significant strides. In controlled factory environments, robotic arms and automated systems are used to assemble modular components, ensuring precision and reducing human error. Some notable robotic applications in prefabricated construction include:
- Automated Assembly Lines: Robotic arms equipped with advanced sensors and AI-driven precision tools can cut, weld, and assemble components for modular buildings at speeds much faster than human workers, improving efficiency while maintaining high accuracy. This is no surprise considering that General Motors first employed a robotic spot welder in the car manufacturing process back in 1961. Today, robotic arms with "vision systems" and other advanced sensors are used for welding, painting, material handling, and other tasks on assembly lines.
- 3D Printing Robots: Large-scale robotic 3D printers use specialized concrete mixtures to print walls and structural components with remarkable consistency, reducing waste and allowing for complex, customized designs that would be difficult to achieve with traditional methods. These robots are already in commercial use for residential and small commercial buildings.
- Automated Material Handling: Autonomous guided vehicles (AGVs) and robotic forklifts help transport heavy materials around prefabrication facilities, reducing the need for manual lifting and improving worker safety by minimizing accidents.
Robotics in Traditional On-Site Construction
Beyond factory settings, robots are also being commercially deployed on construction sites. Some key applications include:
- Bricklaying Robots: Machines like the SAM100 (Semi-Automated Mason) can lay bricks at high speeds, placing up to 3,000 bricks per day—several times more than a human mason—while ensuring precise mortar application, reducing waste, and improving structural integrity. The SAM100 is already in commercial use on various job sites.
- Robotic Excavators and Earthmovers: Companies like Built Robotics have developed self-driving construction equipment that can handle grading, excavation, and trenching with minimal human supervision. These machines use GPS, AI, and sensors to navigate job sites, improving productivity while reducing the need for human operators in hazardous environments. Built Robotics' autonomous equipment is already being commercially deployed.
- Rebar-Tying Robots: Machines like TyBOT automate the process of tying rebar for reinforced concrete structures. This task, which is typically labor-intensive and time-consuming, is completed more efficiently and consistently by robots, freeing up workers for other tasks and speeding up construction timelines. TyBOT is actively being used in the field today.
- Demolition Robots: Remote-controlled demolition robots, such as those from Brokk, are revolutionizing hazardous demolition work. These machines, equipped with hydraulic breakers, crushers, and shears, can safely demolish structures in environments that are too dangerous for human workers, such as after fires or in structurally compromised buildings. These robots are in widespread commercial use and are valued for their ability to operate in confined spaces while reducing worker injury risks.
- Drones for Site Inspection: Unmanned aerial vehicles (UAVs) equipped with high-resolution cameras and LiDAR sensors are used to survey construction sites, track project progress, and identify safety hazards in real-time, reducing the need for costly and time-consuming manual inspections. Construction drones are widely used in the industry today.
Humanoid Robots in Construction Industry
Humanoid robots are gradually being tested in the construction industry, though their commercial use remains in its infancy. These robots, designed to mimic human movement and behavior, offer potential for improving safety, efficiency, and precision in construction tasks. Some of the key applications and demonstrations of humanoid robots in construction are currently occurring in various parts of the world, with a focus on enhancing labor capabilities and reducing risks associated with physically demanding jobs.
In Japan, one of the global leaders in robotics, companies have begun experimenting with humanoid robots for construction purposes. Notably, the Japanese construction company Shimizu Corporation has been testing a humanoid robot, "Kensetsu-robot," designed to carry heavy materials, assist in dangerous tasks, and even help in high-rise building projects. These robots could handle repetitive tasks like carrying and lifting, which traditionally place a strain on workers. By doing so, they could minimize the risk of injury, enhance productivity, and free up human workers to focus on more complex tasks that require decision-making.
In the United States, Boston Dynamics has created a variety of robots capable of performing construction-related work. While the company is more focused on industrial robots that are not strictly humanoid, their development of robots like "Spot," a quadruped robot, showcases the feasibility of using robots in construction settings. These robots are designed for site inspections, surveying, and even material handling, which is a precursor to humanoid robots entering the scene.
Additionally, several startups and research institutions are exploring the role of humanoid robots in construction. For instance, the European Union’s Horizon 2020 project is looking at how humanoid robots can help in tasks such as painting, cleaning, and welding in construction environments. These trials aim to prove that robots can work alongside human teams, handling hazardous tasks to improve safety and reduce labor costs.
The global humanoid robot market is expected to grow significantly in the coming years, with Goldman Sachs projecting a market value of $38 billion by 2035. While humanoid robots in construction are still largely in the testing and demonstration phase, their potential is clear. As technology advances, these robots could become invaluable tools in the construction industry, aiding workers while performing dangerous or monotonous tasks with greater precision and efficiency.
Emerging Robotics Research and Future Trends
The future of robotics in construction is promising, with researchers and companies working on even more advanced applications. Some of the emerging technologies to watch include:
- Humanoid Construction Robots: Research is underway to develop humanoid robots capable of handling delicate tasks such as drywall installation, painting, and finishing work. These robots are designed to work alongside human workers rather than replace them, improving overall job site efficiency.
- Exoskeletons for Workers: Wearable robotic exoskeletons enhance worker strength and endurance, reducing physical strain and the risk of injuries caused by repetitive heavy lifting or strenuous tasks.
- AI-Powered Collaborative Robots: Advanced AI algorithms will enable robots to adapt to dynamic construction site conditions, learn from their surroundings, and collaborate with human workers more seamlessly, improving overall workflow efficiency.
The Road Ahead
While robots will not replace human workers anytime soon, they will continue to play an increasing role in construction, improving efficiency, safety, and precision. As technology advances, companies that embrace robotics will gain a competitive edge, benefiting from reduced costs, faster project timelines, and improved quality control.
Several heavy industries, similar to the construction industry, are increasingly adopting robots to improve efficiency, safety, and precision. These industries range from manufacturing and mining to oil and gas, where robots are being used for a variety of tasks, from routine maintenance to hazardous operations. Below are some key heavy industries where robots are now commercially used:
1. Manufacturing Industry - The manufacturing sector, especially in automotive and electronics production, has long been a leader in adopting robotic technologies. Industrial robots in this sector are used for tasks like assembly, welding, painting, and material handling. Companies like Toyota, Volkswagen, and Tesla have integrated advanced robotics into their assembly lines to increase speed and accuracy while reducing human error. Additionally, collaborative robots (cobots) are being introduced to work alongside humans, handling repetitive or physically demanding tasks, which reduces worker fatigue and the risk of injuries.
2. Mining Industry - In the mining sector, robots and autonomous systems are increasingly being used to enhance productivity and reduce the dangers posed by harsh environments. Autonomous vehicles, such as Komatsu’s Autonomous Haulage Systems, are already used for hauling materials, allowing for continuous operation in mines without human drivers. Drones are also used for surveying and monitoring mining sites, while robots are being employed for tasks such as drilling, excavation, and even underwater mining. These robots not only reduce the risk of accidents but also improve efficiency in operations where human access might be restricted.
3. Oil and Gas Industry - The oil and gas industry has embraced robotics for exploration, maintenance, and inspection, particularly in hazardous environments such as deep-sea drilling rigs or high-risk areas of oil refineries. Underwater drones, like Schilling Robotics' ROVs (Remotely Operated Vehicles), are commonly used for inspecting underwater pipelines and rigs, where human divers would be at significant risk. In addition, robots are employed for tasks such as routine equipment inspection, leak detection, and even performing repairs in dangerous environments, ensuring that human workers are kept out of harm's way.
4. Agriculture - In agriculture, robots are increasingly used to improve efficiency and safety in activities such as harvesting, planting, and pest control. Autonomous tractors, drones, and harvesters are already performing tasks like soil cultivation, crop monitoring, and fruit picking. For example, FFRobotics has developed a robot capable of picking apples, reducing labor costs and improving harvest efficiency. These robots help to reduce the physical demands on workers and minimize human exposure to potentially dangerous chemicals or machinery.
5. Logistics and Warehousing - Logistics and warehousing are increasingly adopting robots to handle material transportation and inventory management. Automated guided vehicles (AGVs) and robotic arms are used by companies like Amazon, Alibaba, and Walmart to move goods, organize warehouses, and pack orders. Robots in this industry help to minimize manual labor, enhance inventory accuracy, and speed up order fulfillment, all while reducing the risk of workplace injuries.
6. Aerospace Industry - The aerospace industry uses robots for tasks such as assembly, inspection, and maintenance of aircraft. Companies like Boeing and Airbus utilize robotic arms for assembly processes, such as drilling, fastening, and installing parts. These robots can work in difficult or hazardous conditions, reducing human error and ensuring precise and consistent quality in aerospace manufacturing.
7. Energy Industry - Robots in the energy sector, particularly in renewable energy, are used for inspecting and maintaining equipment such as wind turbines and solar panels. For example, robots are deployed to clean solar panels or inspect wind turbines for damage in remote or dangerous locations. In nuclear energy, robots perform routine inspections and maintenance of reactors, handling hazardous materials or performing tasks in radioactive environments.
8. Transportation Sector - West Japan Railways has been utilizing a massive 20-foot tall humanoid robot to assist with train line maintenance and other railway-related tasks. However, the robot does not operate autonomously; instead, it is controlled by an operator from a cockpit. The robotics company Jinki Ittai Corp has mounted the upper body of a humanoid robot onto a truck, allowing the robot to be used for mobile applications in train line maintenance. Without the truck, the robot stands about 20 feet tall. It features powerful limbs and hands, each equipped with a two-finger gripper. The span of its arms reaches approximately 40 feet.
These industries are leveraging robots not only to enhance productivity but also to reduce the risks associated with dangerous tasks, improve precision, and address labor shortages. As technology continues to evolve, robots will likely play an even larger role in these sectors, contributing to safer and more efficient operations.
As robotics continues to evolve, the construction industry is set to become safer, more efficient, and more innovative. The coming years promise exciting advancements that will redefine the way buildings are designed and constructed. Advancements in AI and robotics are expected to further enhance the capabilities of humanoid robots, making them even more versatile and capable.
References - Here are some sources providing further insights into robotics in construction:
- Construction Robotics - https://www.construction-robotics.com/buildbetter/
- Built Robotics - https://www.builtrobotics.com/
- 3D Printing in Construction - https://www.3dnatives.com/en/3d-printing-construction-090720204/
- SAM100 Bricklaying Robot - https://www.robotics.org/content-detail.cfm/Industrial-Robotics-News/SAM100-Bricklaying-Robot/content_id/7438
- TyBOT Rebar-Tying Robot - https://www.tybotllc.com/
- Drones in Construction - https://www.constructiondive.com/news/drones-in-construction-industry/
- Brokk Demolition Robots - https://www.brokk.com
- Robotic Bricklaying Technology (Demo Project & Video)- https://www.fbr.com.au/view/news-articles/20250305092829
- West Japan Railways 20-foot tall humanoid robot for Railway Maintenance - https://www.borntoengineer.com/mega-machines-japan-unveils-colossal-humanoid-robot-for-railway-maintenance
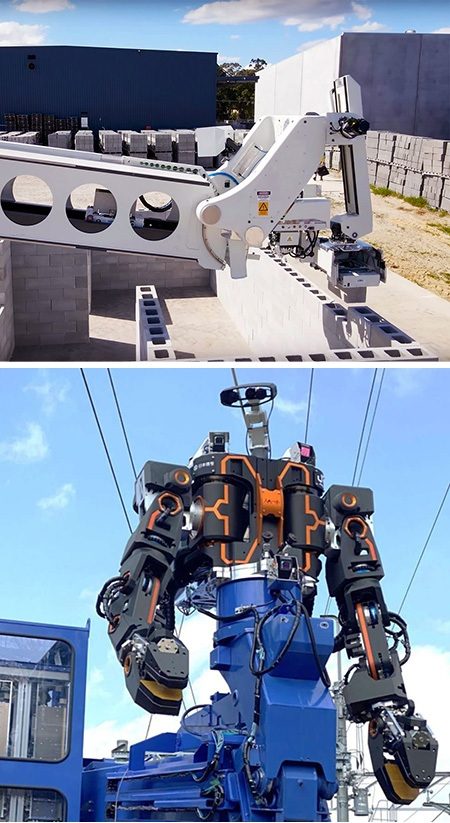